Table of contents:

Video: Concrete Mix For Cellar Construction, Concreting And Cellar Construction
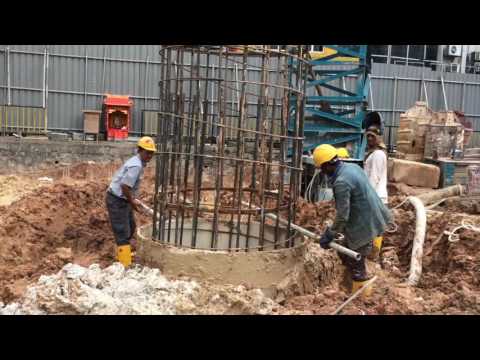
2024 Author: Sebastian Paterson | [email protected]. Last modified: 2023-12-16 13:47
Often in popular magazines there are articles about the construction of various buildings and structures, in which the authors share their "experience", ignoring the elementary requirements of building codes and regulations (SNiP). So, in a magazine popular among gardeners, an article was published about "packing" - the device for waterproofing the cellar. The author, who recommended a single-layer glued waterproofing, obviously did not know about the existence of building codes and regulations (SNiP), regulating not only the design requirements, but also the technology of its construction.
Based on my experience, I can draw the following conclusions:
- Such waterproofing is not able to protect the cellar even from dampness - this is money and labor wasted.
- Not a single gardener will dare to bury his cellar below the groundwater level, therefore, the need for expensive 2-3 layers of glued insulation is unnecessary.
I believe that it is enough to choose the correct composition of the concrete mixture so that, as a result of its correct laying in the formwork, you get a cellar with waterproof structures. This is what this article is about. Let's start with the selection of the composition of the concrete mixture (cement: gravel (crushed stone): sand: water). Our goal is to obtain the required strength (grade) and density (porosity) of the concrete stone.
Concrete mix for building a cellar
Cement. In terms of the quality and resistance to soil corrosion of concrete, Portland cement of grade 300-400 will be the best.

To prepare one m2 of concrete mix you will need:
Water. The strength of concrete also depends on its water content. An increase in the water additive relative to its optimal amount reduces the strength of concrete due to the creation of increased capillary porosity of the hardened cement stone (cement: sand: water) in concrete and, as a rule, worsens the water resistance of concrete. For the preparation of concrete operating in an aggressive medium of medium (wet and wet soils), the maximum water-cement ratio (W: C) for dry aggregates should be taken no more than w / c = 0.5, i.e. water will require exactly half of the weight of the cement (for 1 kg of cement - 0.5 liters of water).
Placeholders. Coarse aggregate - crushed stone or gravel from hard igneous or sedimentary rocks. For concrete M-150 and higher, the ultimate compressive strength of the aggregate is not less than 600 kg / cm2. The optimum grain size for concrete with fine aggregates is 10-40 mm. The maximum grain size is 70-80 mm, but not more than 1/3 of the thickness of the concrete structure. The best result in terms of cement consumption and workability, i.e. the mobility of concrete is achieved on crushed stone or gravel with a grain size of 5-10, 10-20, 20-40, 40-70 mm.
Fine aggregate - coarse sand, medium size. For fine (not dusty) sand, cement will need 5-7% more. In general, sand for the preparation of concrete will take so much to fill all the voids in the coarse aggregate - crushed stone (gravel), and in order for the concrete mixture to be more mobile, sand should be taken 5-10% more in order to expand the gap between the grains of the coarse aggregate.

Figure: 1. Working joint of wall and bottom
1- paint waterproofing;
2- preparation cement screed;
3- crushed stone preparation.
Placement of concrete mixture into the structure (concreting)
In order for the concrete mixture to turn into a waterproof, equally strong in any place (section) and a truly monolithic structure, it must be properly laid. First of all, you need to remember the main requirement: in order to ensure the quality of the structure created from concrete, the concreting process must be continuous. The concrete mixture in the bottom slab should be laid in a strip along the entire length (width) of the slab to its entire height (thickness), and concrete is placed in the wall formwork in uniform layers along the entire perimeter of the wall with a thickness equal to the working height of the vibrator. In the case of compaction of the concrete mixture by hand by bayonetting, the layer thickness should be no more than 300 mm, and the number of punctures when bayoning should be at least 100 per 1 m2 of the layer surface. The time gap during concreting between adjacent layers should not exceed the time of the beginning of the setting (hardening) of the mixture (from 40 minutes to 1.5 hours).
To prevent the concrete mixture from stratifying into fractions during the laying process, the height of the dumping (feeding) of the solution should be minimal. In the wall formwork, the concrete mixture should be laid from two levels: the first at a height of 1 m from the bottom slab, and the second from the floor slab. Working seams and technological breaks in concreting - the first at the junction of the bottom plate with the wall, the second at the junction of the wall with the cellar floor slab. The resumption of concreting after a technological break is possible only after the concrete reaches a strength of at least 15 kg / cm2 (when the edge of the hardened concrete does not crumble under the fingers).
To increase the water tightness of the working seam, before the end of the concreting of the bottom plate along the entire perimeter of the wall, it is necessary to install a waterproof barrier in the form of a strip 200-300 mm wide in the working seam (see Fig. 1). Before resuming concreting, the surface of the working joint must be prepared: clean it of debris, remove the film formed during the hardening of the cement stone from the surface of the hardened concrete with metal brushes or scrapers. At the beginning of laying the concrete mixture, cement mortar of grade 150-200 should be laid over the entire surface of the working joint with a layer of 20-30 mm. At an air temperature of 5 ° C, concrete practically ceases to harden and gain strength. The optimum air temperature for curing is 18 … 20 ° C, high humidity is also desirable. In dry weather, open surfaces of hardening concrete should be covered with damp mats.

Figure: 2. Sectional cellar
Anti-corrosion protection of concrete
The degree of aggressiveness (corrosiveness) in relation to concrete of sandy, clayey, saline soils, depending on humidity, the content of nitrates, organic (humic) substances, varies from low to medium. In rich black soil, peat - up to high. To protect concrete from corrosion and capillary moisture, it is enough to paint its open surfaces with bitumen mastic. Hot bitumen mastic from BN IV bitumen "lays down" very poorly on a cold concrete wall, forming a loose film with caverns. To improve the quality of the coating, at the beginning the concrete surface is primed (painted) with a primer (dissolved in gasoline, molten BN IV bitumen, kerosene and diesel fuel are not suitable), and then painted with hot bitumen mastic created from bitumen of this brand. The film thickness is adjusted to 4 mm in one or two times. A sufficiently strong coating is obtained using cold bitumen mastic and the same primer. For priming the first layer, a composition is prepared 1: 3, for the second 1: 1, and for the third 3: 1 (bitumen: gasoline by volume). Simultaneously with filling the sinuses around the cellar with ordinary soil, the insulation layer is covered with sand (see Fig. 2) to protect the insulation from damage.
Ivan Pavlov, gardener, experienced builder
Recommended:
Planning And Construction Of Rockeries, Selection Of Stone, Arrangement Of Paths And Retaining Walls

Is a rocky garden or rockery a western luxury or a pile of stones scattered in the chaos through which plants make their way?
Elements Of Garden Design, Construction Of Stairs In Rockeries, Types And Construction Of Retaining Walls - 2

Garden design elements that help shape its appearanceLadder construction technology in rockeriesOne of the simplest ways to build a staircase in a rocky garden is dry masonry, which is equally applicable to retaining walls. Construction begins with the laying of the bottom step
How To Build A Small Cellar From Scrap Materials, Creating A Mini Cellar

How to build a small cellar from scrap materials, creating a mini cellarIf you study the available special literature, it turns out that almost all recommendations for creating winter storage facilities for fruit and vegetable products are designed for peasant farms, the areas of which, and therefore the volume of harvests, are many times larger than in summer cottages
Waterproofing Agent For Stone And Concrete Aquarius

You will save up to 30 % on heating by using a waterproof agent for stone and concrete "Aquarius", which does not allow water to accumulate in the walls, thereby increasing their thermal insulation and at the same time protecting them from fungi and bacteria
Concrete Cleaner "Aquarius"

Concrete cleaner "Aquarius" effectively removes blackness, mold, mildew from concrete, brick, stone, slate surfaces and has proven itself perfectly when used in bathrooms, in basements and cellars